The
Thick Coal Seams of South Staffordshire
HD
Poole from The Blackcountryman Magazine Volume 1, Issue
3
The
term "thick coal seam" may convey an impression
that the seam of coal is solid and massive and 8-10 yards
in thickness. It is, in fact not one seam but a number
of separate and distinct seams or layers of coal numbering
from 10-15. The seams have been given names by the miners
who recognised distinctive characteristics in each seam.
It is difficult to give reasons for all the names.
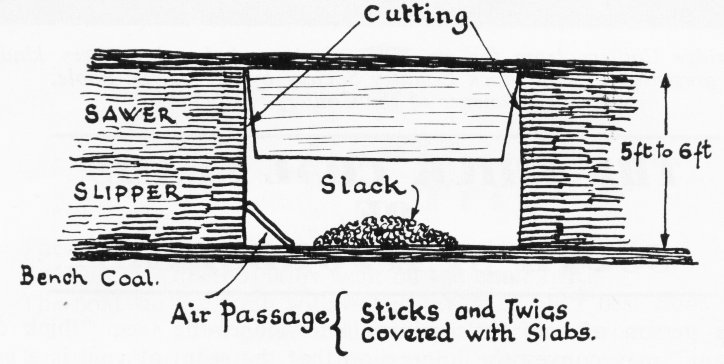
Benches |
This
seam was very often left unworked for, being a strong
coal, it prevented the unwelcome intrusion of the
soft clay-like measures from beneath |
Dice |
Above benches, coal which easily
broke up into cubical pieces and was easy to remove |
Slipper |
Seams of good quality coal |
Sawyer |
Patchells |
Seams about 12 inches thick |
Foot |
Stone |
frequently had a stone or dirt parting on top
of it. This parting varied in thickness and in the
Blackheath district was several feet in thickness,
necessitating working the lower section and then dropping
the stone and using it as the floor for the top section. |
Veins |
Had special markings, not very good coal |
Fine |
coal of better quality |
Brazils |
hard and inferiour in quality. It would break
up into large cubical pieces or blocks, the author
saw a substantial wall built with this material. |
Heath |
Usually the best qulaity of coal.
Evident to the earlier miners who worked considerable
areas of the top section and the Slipper and Sawyer
of the lower section, leaving the middle section to
posterity. |
Floors |
White |
Spires |
Rooves |
The first attempts at working the thick
coal to replace the use of timber for fuel were along
the lines of outcrop onto the surface. It was simply a
question of removing the soil to expose coal. It may be
coal had already been used as fuel because it could be
found on sea beaches where outcrops of seams occur in
cliffs. Waves were the cause of breaking up of the coal
and together with adjacent rock shaped into pebbles of
various sizes. This was known as "sea coal".
Although there were vast quantities of this in the course
of time miners were forced to follow the seam down, and
in order to reduce the amount of spoil to expose the coal,
were forced to begin sinking small shafts. On reaching
coal the shaft was continued but at a gradually enlarging
diameter until reaching the bottom of the seam. These
were known as "bell pits", and the reason can
be seen from the illustration below.
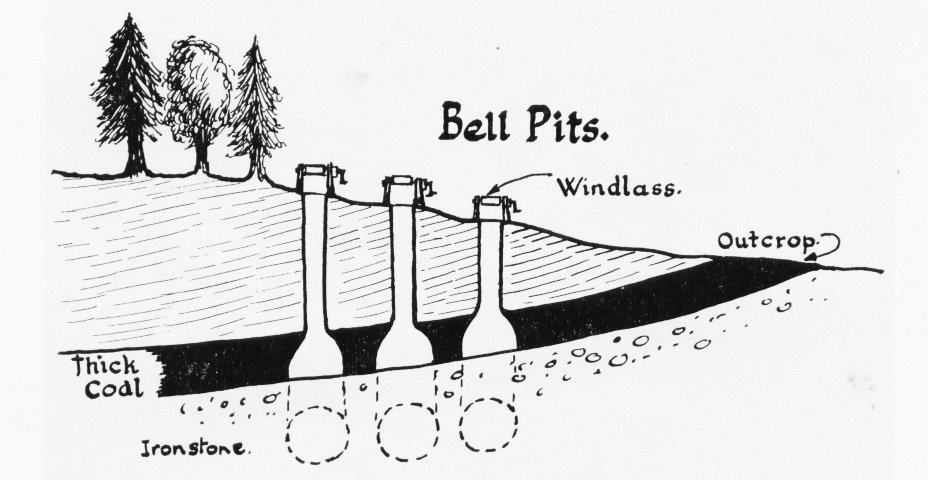
When bell pits had had there day they were
replaced by the sinking of shafts to greater depths and
the introduction of systematic methods of working the
top and bottom of the seam. The miner now became a skilled
craftsman who took great pride in his work and, as rules
and regulations were non-existent, his time was his own
concern. It is most probable his wife worked the hand
windlass to wind the coal to the surface.
The skill and neatness of the miner - probably
from about the 14th century - were researched from first
hand study by the original author of the article. He was
able as a young student to inspect the stalls or working
places, as these were approached by workings from an active
coalmine. The coal being of a strong nature and the height
and width of the stall being small, the working places
were found exactly as left many years before. At this
time any coal was acceptable and the slack or small coal
had a ready market for steam raising. On entering an ancient
stall, one was impressed by the care and precision of
the miner. Vertical and smooth sides; neat undercutting
in the coal to prepare for extraction; an occasional small
recess in the side of the stall to hold his tobacco pipe
in a safe place, also his 3-handled drinking cup of which
examples can be seen in museums in the midlands. A miner's
pick was also found and the writer was impressed by the
heavy weight of this tool.
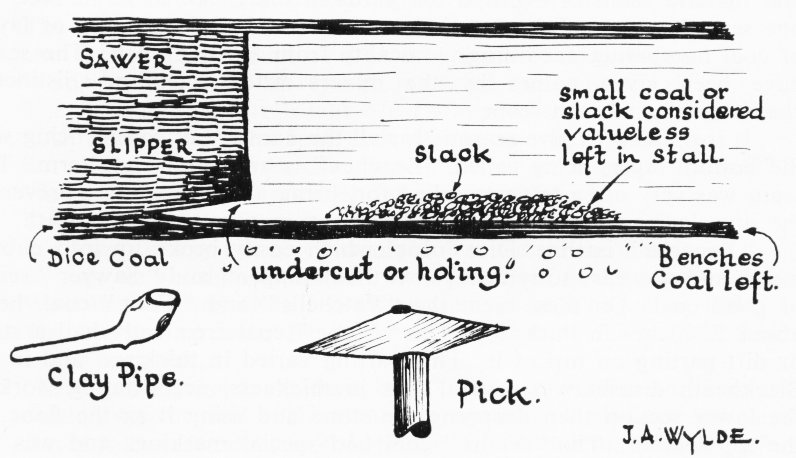
On one occasion a small shaft was found
and bones were exposed. The first thought was perhaps
that these belonged to a miner, but on further investigation
they were found to be of a deer and the small skeleton
of an off-spring. The position of this shaft was carefully
marked on the mining plan and it was found that an old
turnpike road was immediately over it. Just one more incident
in a lifelong fascination with coal!
The author
of this article - HD Poole - was General Manager
of Baggeridge Colliery from 1926 to 1937. The illustrations
used were taken from the article mentioned at the
top of the page. Mr Poole was 90 years old in 1968,
I would like to hear from anyone who could put me
in contact with his family, as I am sure they will
have many memories that they may wish to share.
Mick Pearson
|
Email the web master Mick Pearson:
.
|